- Insights & events
- 4flow studies
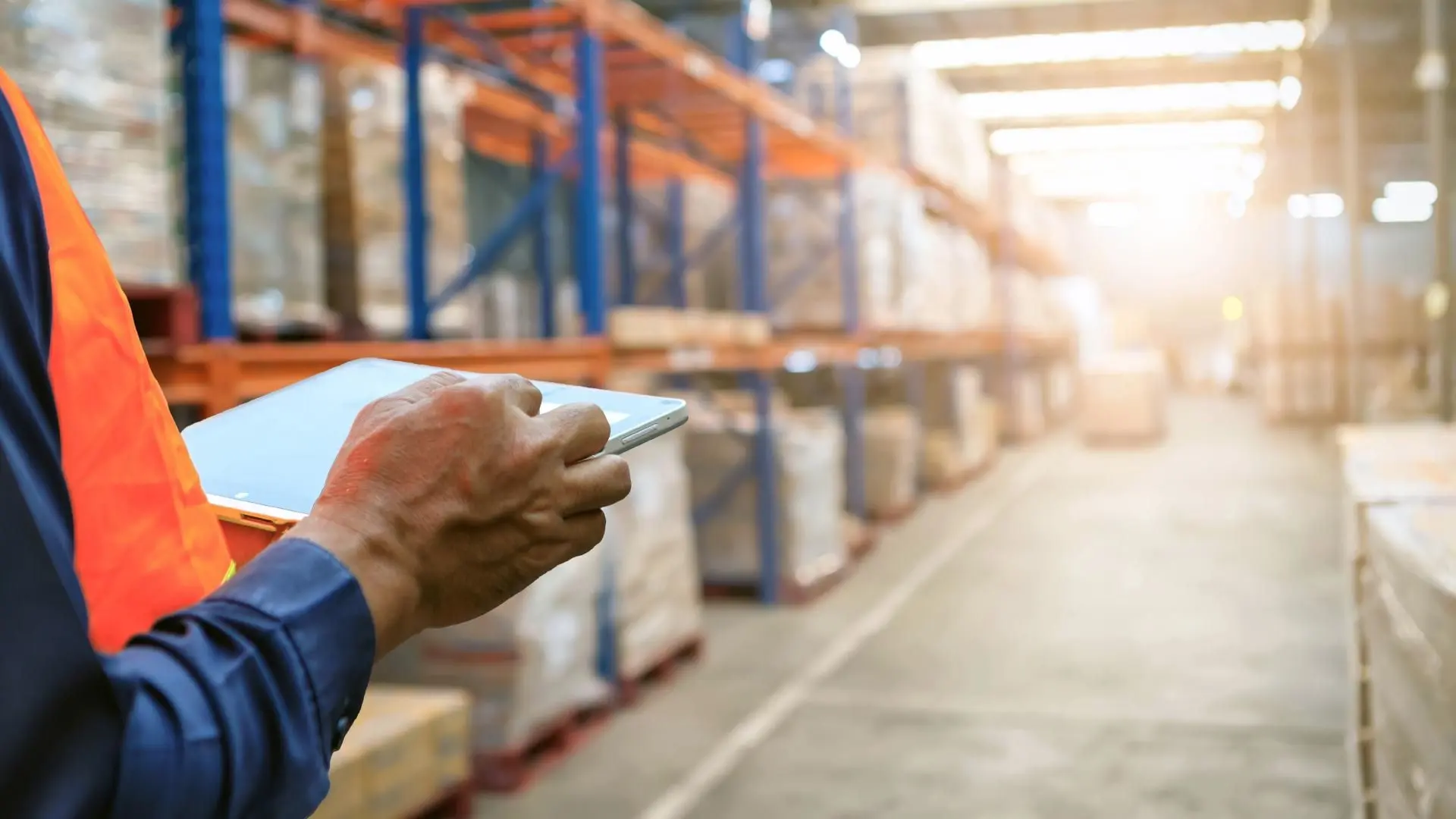
4flow study
Paperless inbound and outbound
Transitioning from conventional to paperless inbound and outbound in the reference warehouse leads to:
At a glance
Transitioning from wide aisle racking to an automated storage and retrieval system (AS/RS) can result in substantial reductions in energy consumption, CO₂ emissions and OpEx.
The case in context
Traditional manual warehouses demand extensive space and a sizable workforce. A limited availability of land and intensifying labor shortages make operation of such warehouses increasingly expensive. As a result, there is growing interest in warehouse automation. Seen from an environmental perspective, manual warehouses tend to have high CO₂ emissions due to their size and reliance on powered industrial vehicles (PIV).
Wide aisle racking, commonly used in manual warehouses, offers a low cost of implementation. It is versatile and compatible with low level order pickers (LLOP) guided by pick-by-voice. However, floor space utilization is low with this storage solution, which leads to larger warehouses and long driving distances in intralogistics processes.
An automated high bay warehouse offers an alternative to enhance floor space utilization and productivity.
A closer look: case details and parameters
For this case we compared the following scenarios:
- Manual reference warehouse: utilizing reach trucks for pallet transportation and putaway and a fleet of LLOP for picking
- Automated high bay warehouse: incorporating automation while maintaining the same building height, using a reduced fleet of reach trucks for pallet transportation, stacker cranes for putaway, and goods-to-person picking, eliminating the need for LLOP
Results
The automated warehouse presents several advantages:
- Approximately 20% less floor area needed for storage thanks to the reduced aisle width of the AS/RS, without affecting the total storage capacity
- 65% less time required for transportation and putaway of inbound pallets due to automation of the process with the AS/RS
- 35% less picking time on average due to shortened distances and goods-to-person picking
- 50% fewer reach trucks and no LLOP needed due to automated putaway and goods-to-person picking
- 35% lower full-time equivalent (FTE) requirements due to reduced distances and higher efficiency of goods-to-person picking
- Over 75% fewer light fixtures needed, as AS/RS areas have reduced lighting requirements
- Over 35% lower electricity consumption and CO₂ emissions due to significant reductions in PIV, lighting quantities and physical footprint
Despite the significant upfront investment, the AS/RS solution yields more than a 5% reduction in operating expenses over a 15-year period.
Evaluation: greatest OpEx savings in study and moderate emissions reduction
Changing the storage and picking technology offers the largest potential for OpEx savings within this case study framework. The impact on CO₂ savings, however, is moderate compared to other cases. For this reason, as well as the high complexity, the potential for disruptions during implementation of the solution in an existing warehouse, and the high upfront costs, we recommend considering this measure mainly on its economic merits. This is especially true with a greenfield project, where a build-to-suit building solution can help a business realize the full potential of automation technology – for example, with a taller AS/RS silo section to increase storage density and reduce the number of stacker cranes required.
Key results
4 tons total CO₂ savings over 15 years - <1% of total warehouse CO₂ emissions €42,000 total cost savings over 15 years