- Insights & events
- Success stories
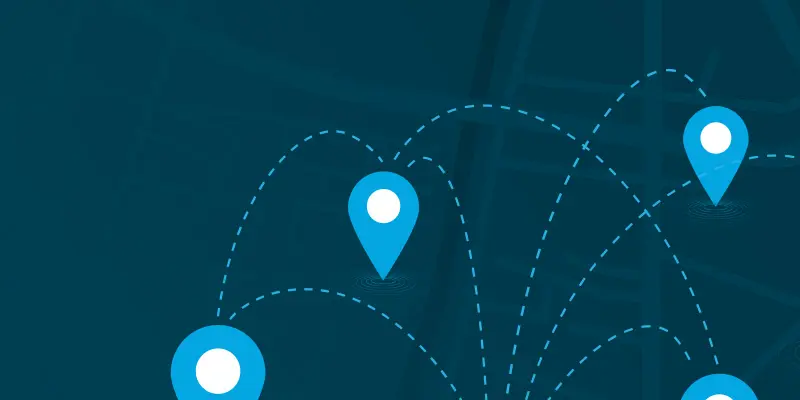
Automotive manufacturing
Success story
Track & Trace
4flow collaborates with vehicle manufacturer to develop and roll out a Track & Trace system for intercontinental supply chains
Enabled by big data and the increasing automation of operational processes, businesses from a wide variety of industries rely more and more on shipment tracking. Implementing a Track & Trace system makes it possible to automatically determine both the current and past locations of specific objects. The benefits include an increase in end-to-end transparency across the entire supply chain and the ability to identify levers for cost savings.
Track & Trace is well suited to highly complex networks such as the intercontinental PbP (part-by-part) and CKD (completely knocked down) supply chains common in the automotive industry. This is where many different partners are involved in a shipment between consolidation points and overseas plants, using different modes of transportation. In such a complex environment, integrating Track & Trace into long supply chains ensures that end-to-end transparency is maintained.
Working together with 4flow, Mercedes-Benz AG successfully and efficiently carried out an initial Track & Trace rollout. Thanks to an operations model designed by 4flow, coupled with user training focused on the long term, the automotive manufacturer is now well equipped to connect additional shipping lanes to the system.
Design, implementation and quality assurance
The implementation of a global Track & Trace system, which is accessible to both internal and external project partners, requires an end-to-end planning approach. To quickly achieve organizational involvement as well as the acceptance of future end users, key questions were addressed before the rollout: Who are the main users and what functionalities will help create added value? At what level of detail should information be available and who will provide the necessary data in the quality required?
With the objective to design the most seamless rollout possible, 4flow was asked to create a Track & Trace operations model. The central tasks were to define the different functionalities, develop a model of roles and responsibilities and generate requirement specifications. In constant focus were the potential optimization areas developed collaboratively in the project: productivity, inventory, transportation cost, investment, and throughput time. The successful collaboration was continued in further Track & Trace system rollout projects – with the objective to connect new supply chains. As a result, even more consolidation points, logistics service providers, transportation service providers of all modes as well as overseas plants were integrated in the Track & Trace system. In addition, throughout the course of the rollout, processes to ensure the required data quality were established.
From operations model to integrating data from internal and external process partners
The operations model was developed based on expert workshops focused on the requirements of the operations processes for intercontinental supply chains. Analyzing the input from different areas of expertise enabled 4flow to define basic Track & Trace functionalities, coordinate them with experts and include them as requirements for the system in the form of user stories.
An example of a basic Track & Trace functionality is an alert, which serves to proactively inform users about irregularities in the operations processes. For example, a “container not loaded” alert promptly and actively informs those responsible for operations when a container has not been loaded onto a ship as scheduled. For the basic functionalities, 4flow created a model of the roles and responsibilities defining the activities of internal and external process partners in the operational processes. For the “container not loaded” alert, for example, precisely who is to be informed about an exception in the schedule and the follow-up process steps to be initiated, is predefined.
Fully tracked supply chain from Europe to the USA
Goods are shipped from Europe to the US with a fully connected supply chain. By successfully connecting consolidation points, logistics and transportation service providers and incoming goods at the overseas assembly plant to the Track & Trace system, process partners in Europe and the US can track shipments entirely within a single system environment. Previously, this had been handled by tracking solutions from external partners and various in-house ERP systems.
Integrating internal ERP systems to an end-to-end Track & Trace solution also creates, for the first time, transparency on material inventory for each location along the long supply chain. Furthermore, updates on the Estimated Time of Arrival (ETA) in the overseas plant’s MRP (Material Requirement Planning) run can be automated and used in real time. This is of particular benefit to the automotive manufacturer in the event of supply chain disruptions, such as the emergency situation triggered by the Covid-19 pandemic.
Proven procedures in an agile project environment
Developing and rolling out a Track & Trace system requires a strong IT focus and was carried out using the scrum method. 4flow supplemented its proven project approach with agile working methods. For example, operational requirements were documented in structured expert workshops involving the customer‘s internal and external process partners. For the technical development, 4flow transferred the requirements to an agile IT environment – including user stories, refinement, testing and user acceptance. 4flow‘s diverse experience in SAP projects was beneficial, as the Track & Trace setup implemented by the customer is based on an SAP system.
In addition to cross-functional and cross-organizational collaboration in all project phases, a decisive project success factor was 4flow’s comprehensive project management. The involvement of all process partners – supply chain managers and IT experts from internal and external partners – was key to this success.
Sounds interesting?
Contact usAt a glance
Customer: Mercedes-Benz AG
- Industry: Automotive manufacturing
Project scope:
- Initial rollout of an end-to-end Track & Trace system along the entire supply chain and integration of internal ERP systems
Results:
- Complex shipments are trackable within a single system landscape
- Transparency about material inventory for each location along the entire global supply chain
- Process exceptions are identifiable to then initiate measures to secure plant supply